He’s worked for Rolls Royce, Velan and others over the past 45 years
From the time he lived in Beirut until arriving in Canada in 1966, Jack Awakim had begun to think carefully about what he wanted to do with his life.
Would he turn professional as a boxer, remain a presser at a Montreal suit manufacturer, or become a skilled toolmaker and machinist for Montreal’s burgeoning engineering and aerospace industries?
In the end, the decision wasn’t difficult for the long-time Chomedey resident, now semi-retired at age 77 from a sometimes challenging but frequently interesting machining and toolmaking career.
As Jack related in an interview with the Laval News, his brother had come to Canada three years earlier to work as an aircraft mechanic and invited Jack, who was then 21, to join him. As early as age nine in Lebanon, Jack had developed an interest in boxing.
Choice of a career
So, by the time he arrived in Montreal, he was appearing as a contestant in amateur boxing tournaments at the Paul Sauvé Arena, on the same bill as local boxing stars like Donato Paduano, who competed in the men’s welterweight event at the 1968 Summer Olympics.
One of Jack’s first jobs in Montreal was as a suit presser at Peerless Clothing, the largest manufacturer of men’s and boys’ tailored clothing in North America.
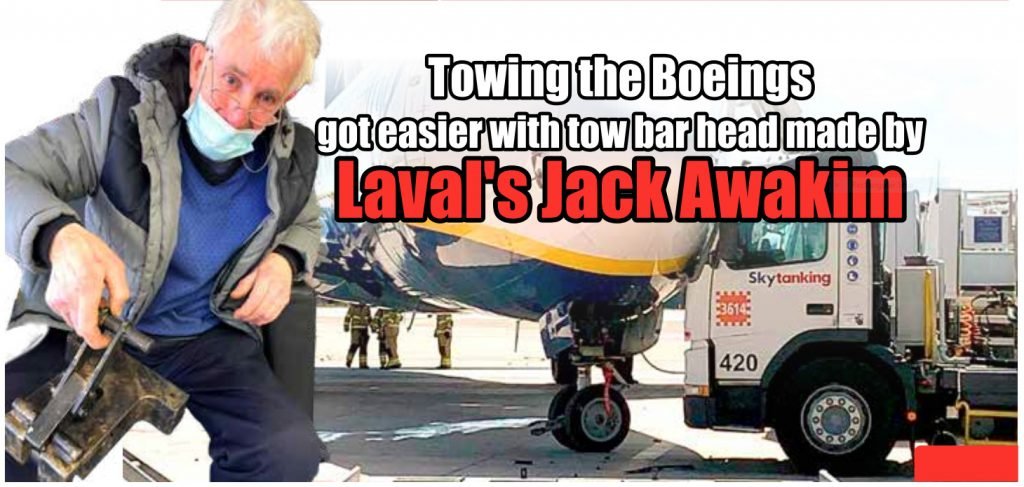
However, by the mid-1970s, an acquaintance he’d met through his boxing connections saw that Jack seemed to have potential to do more meaningful work. So, he invited him to drop over for a job interview at J & R Weir, a shipbuilding company located at that time along the docks in Montreal’s east end.
Rolls Royce, Velan and Nordair
Although he initially started out as a cleaner, that became Jack’s first introduction to die-making and parts machining. For the next five years, he studied at a Montreal technical skills institute, finally becoming certified. He went on eventually to work for companies that included Velan Engineering, Rolls Royce Canada, Eastern Airlines and Nordair, although also as a freelancer out of his own office and workshop.
Tool and die makers are traditionally regarded as skilled artisans or craftspeople. They work from technical drawings provided by engineers or technologists, then cut and shape metal materials using a range of manually, or, more often today, computer-controlled machines than include lathes, jigs, grinders and drill presses.
However, precision in this particular trade is so acutely important that the sensitive measuring tools number in the dozens. To illustrate the point, Jack refers to what has become a textbook case among engineers for structural failure caused by minutely imprecise measurements.

Lessons from Shuttle Challenger
The explosion of the Space Shuttle Challenger happened in January 1986 because of the failure of two O-ring seals in a joint in the spacecraft’s solid rocket boosters. “Half a thou is something you cannot see just with your eyes,” Jack said, referring to a portion of a thousandth of an inch discrepancy that was discovered afterwards in the fitting of the O-rings.
As a result, and also because of record-low temperatures on the day of the launch, fluids and gases made their way through the tiny breach, igniting an external fuel tank on the Challenger.
Among the more interesting pieces Jack has made is a series of tow bar heads produced for an air transport company with fleets of Boeing 747, Boeing 727 and Fokker 100 airliners. When on the ground, aircraft sometimes need to be towed to maintenance or into position. But as aircraft usually have their own proprietary tow bar mechanism, Jack’s was relatively unique in that it could be used on the three airliners.
Well-rounded training
Mind you, the business has changed enormously since Jack began more than four decades ago. With the advent of computing in the manufacturing fields, tool and die makers have had to increasingly add skills in computer numerical control (CNC), computer-aided design (CAD) and computer-aided manufacturing (CAM) to their range of knowledge. However, today’s tool and die makers are generally also required to know the traditional skills in order to be well-rounded.
The business has changed enormously since Jack began more than four decades ago
Mathematics is an integral part of being a machinist. As such, students also learn the basic concepts of equations, formulas and trigonometry as applied to machining problems. As technical drawings and blueprints form the basis from which a machinist works to manufacture simple and complex parts, students also learn how to interpret industry-standard drawings and accurately identify various critical features and specifications.
Many job opportunities
Those who decide to follow this calling can become qualified for a range of job descriptions, including Lathe Operator, Reamer Machine Set-Up Operator, Machine Shop Layout Worker, Precision Grinder, Drill Press Set-Up Operator, Set-Up Operator, Milling Machine Operator and Machine Shop Maintenance.

While Jack says the business has been good for him, allowing him to live and raise a family in Chomedey, his advice to aspiring future die makers and machinists is that a good amount of the skill and craftsmanship will often be acquired only after you’re on the job and gaining experience. “They teach you the basics in school, but there are still many other things they don’t teach you,” he said.